Manufacturing process
Manufacturing-
process
Quality – made in Bergisch Gladbach.
With an impressive machine park and a lot of attention to detail.
Door interlocks
How it’s done.
Fertigung Türverriegelungen
1. Machining center for the housings of our door interlocks
1. Machining center for the housings of our door interlocks
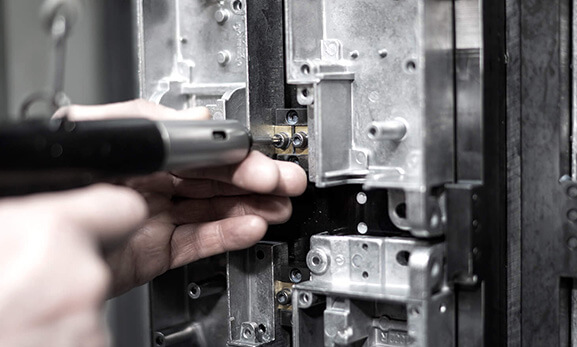
1.The photo shows the equipment of the CNC-milling center.
The rough cast housings for our door interlocks are prepared for final assembly in our FH4000 machining center. For this purpose, two cubes are alternately fitted with untreated housings and transferred into the machining center.
During the processing of the equipped cube, the removal and replacement of the other cube are made in parallel.
2. Hydraulic press
2. Hydraulic press
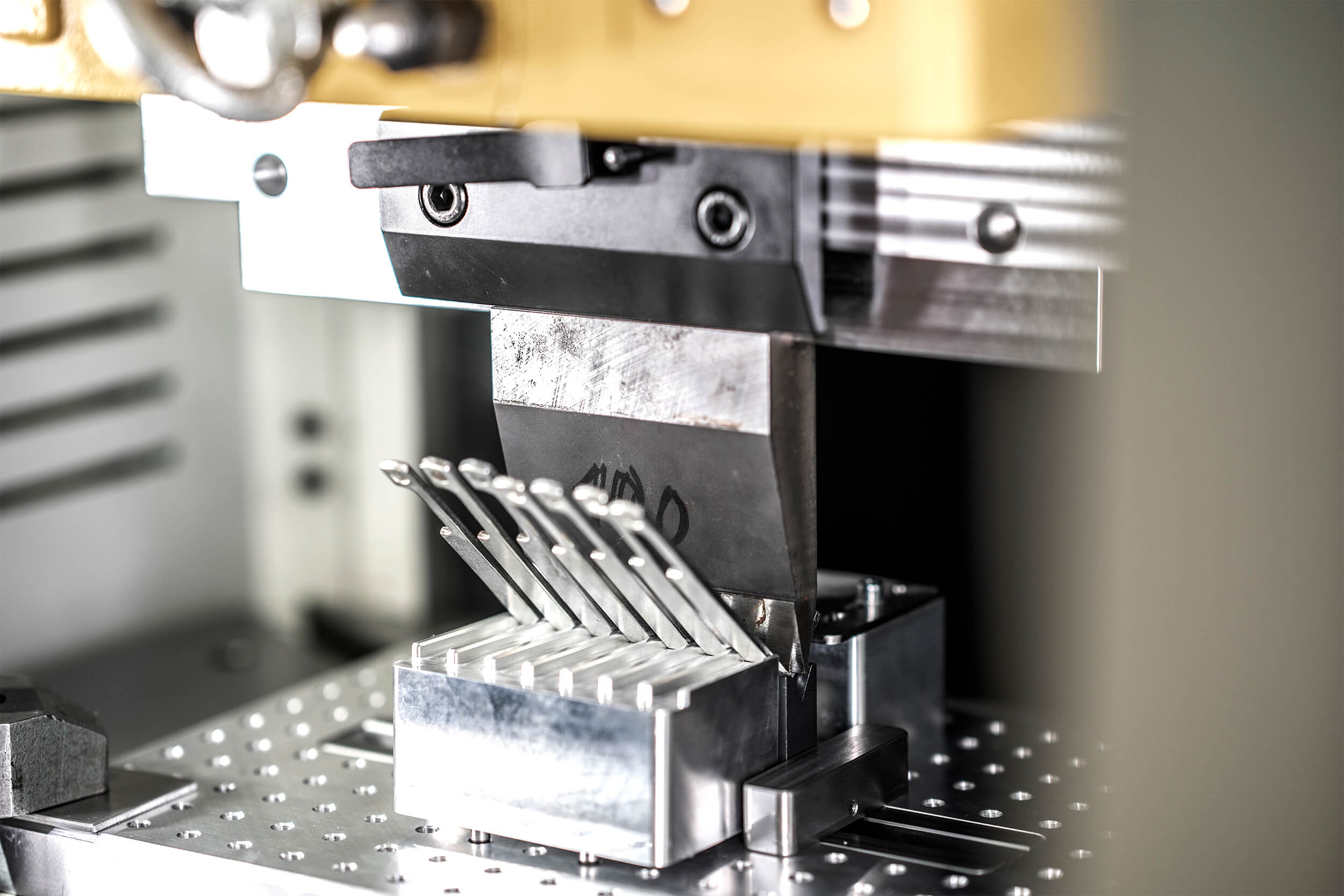
The photo shows the hydraulic press in action.
On the hydraulic press the pull rods to operate the door interlocks are bent.
3. Milling work in the prefabrication
3. Milling work in the prefabrication
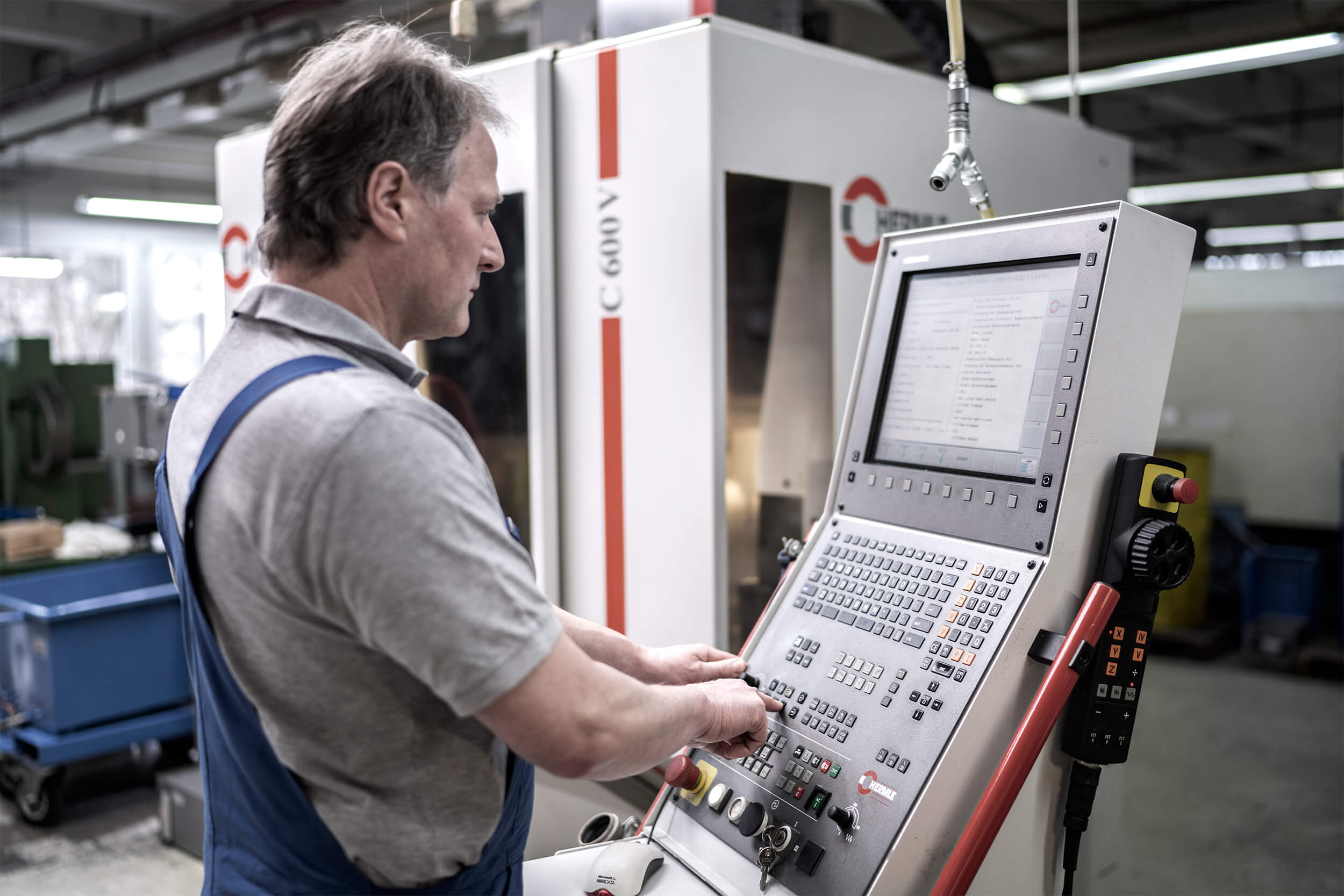
The photo shows the programming of the CNC-milling machine.
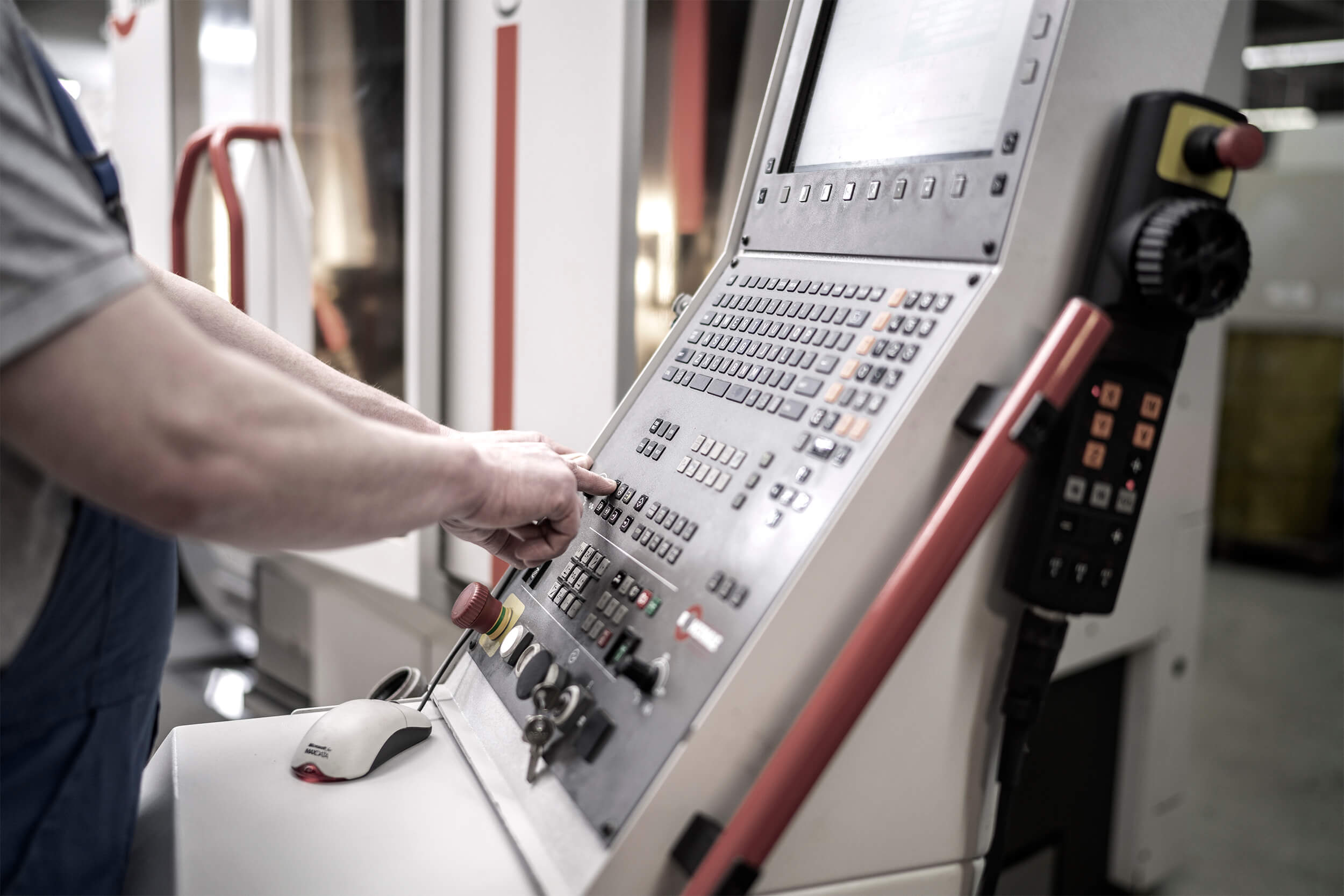
The photo shows the programming of the CNC-milling machine.
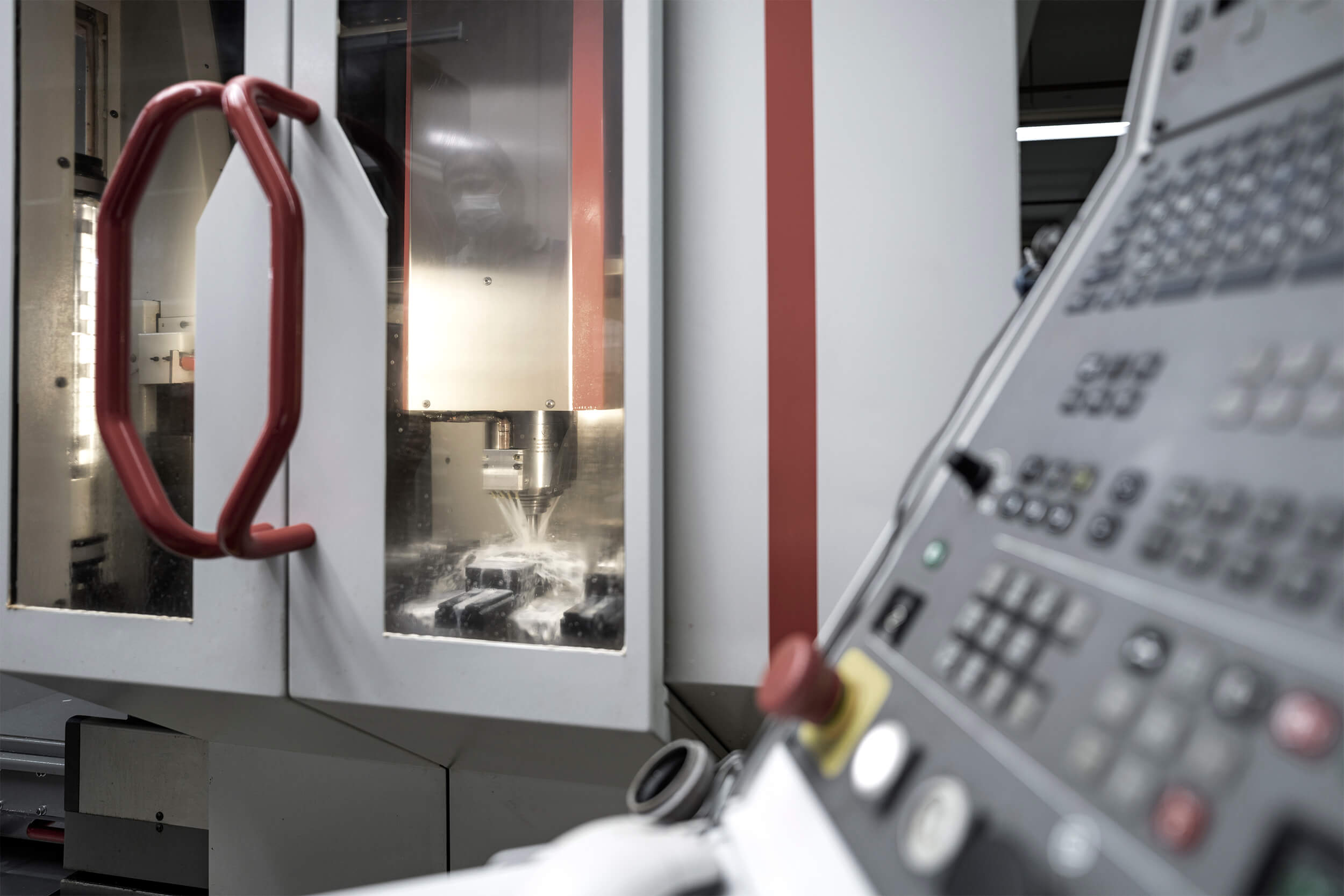
The photo shows the CNC-milling machine in action.
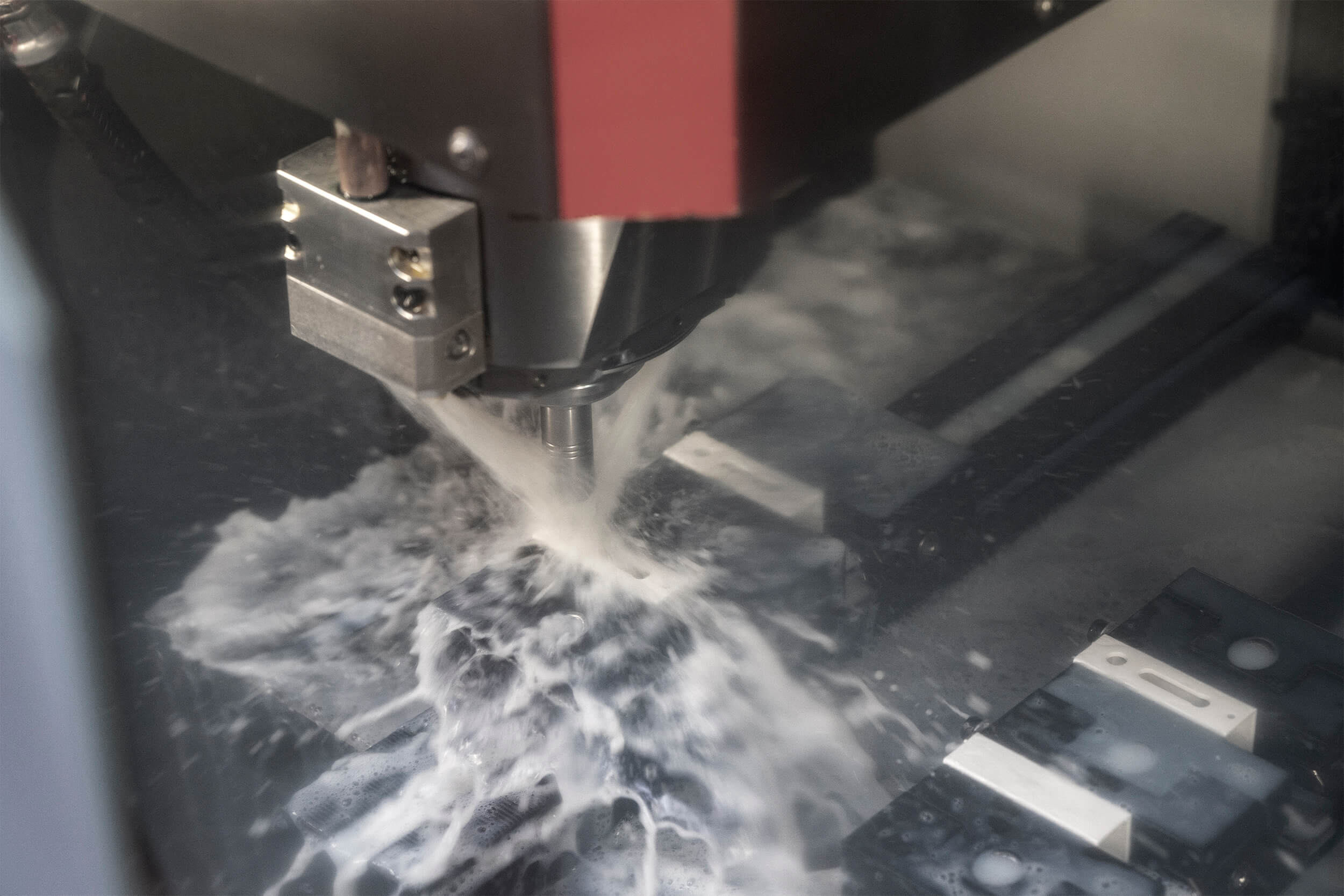
The photo shows the CNC-milling machine in action.
4. Final assembly of the door interlocks
4. Final assembly of the door interlocks
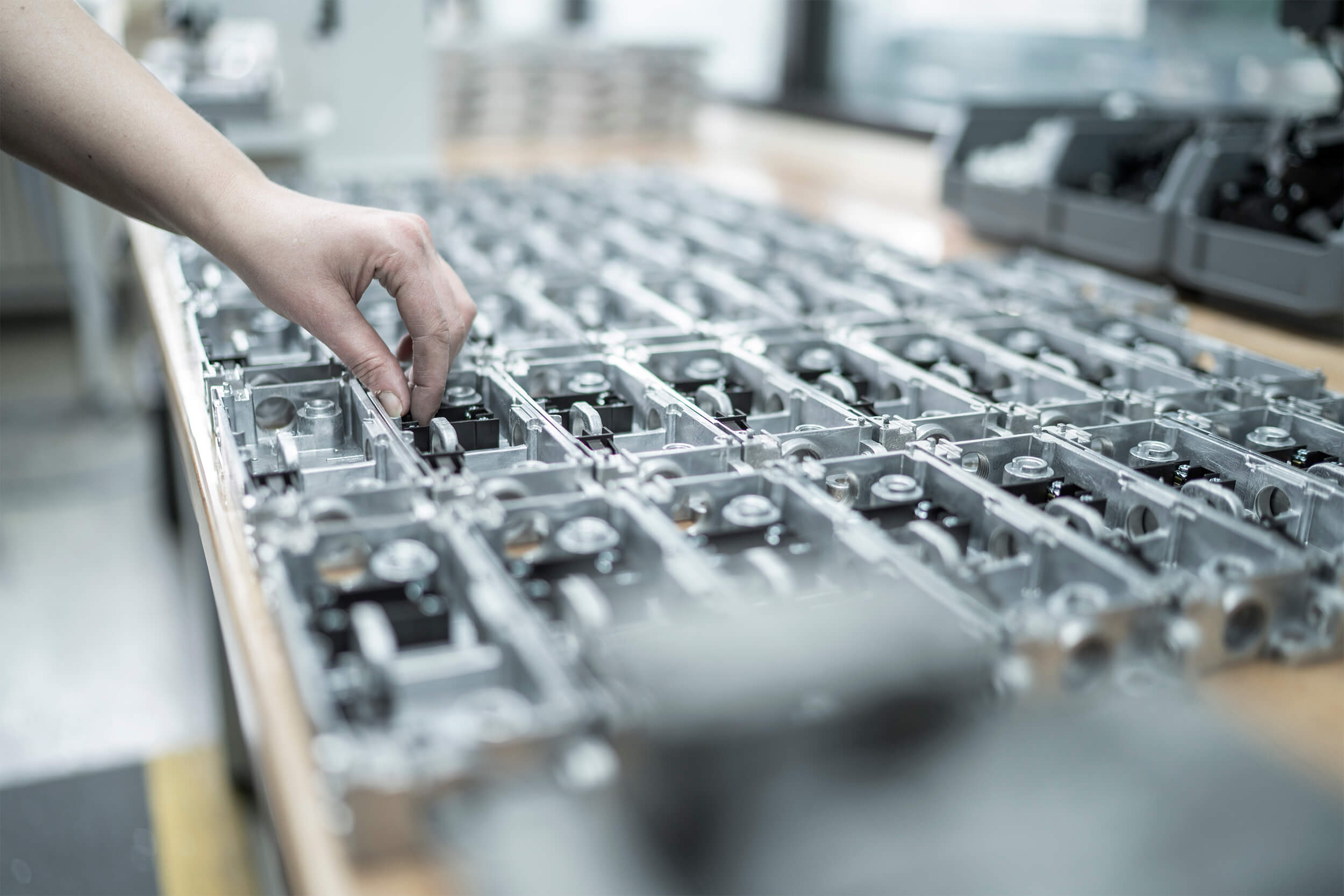
The photo shows a skilled worker in the final assembly.
The finished housings go together with the prefabricated locking bolts and other components for the door interlocks (such as toothed levers, roller levers, locking pins, contact inserts, etc.) in the final assembly.
There the door interlocks are finalized according to customer’s orders and component testing and quality control is made.
OPERATING PANELS
1. Sheet metal processing center
Fertigung Tableaus
1.Sheet metal
processing center-
1.Sheet metal processing center
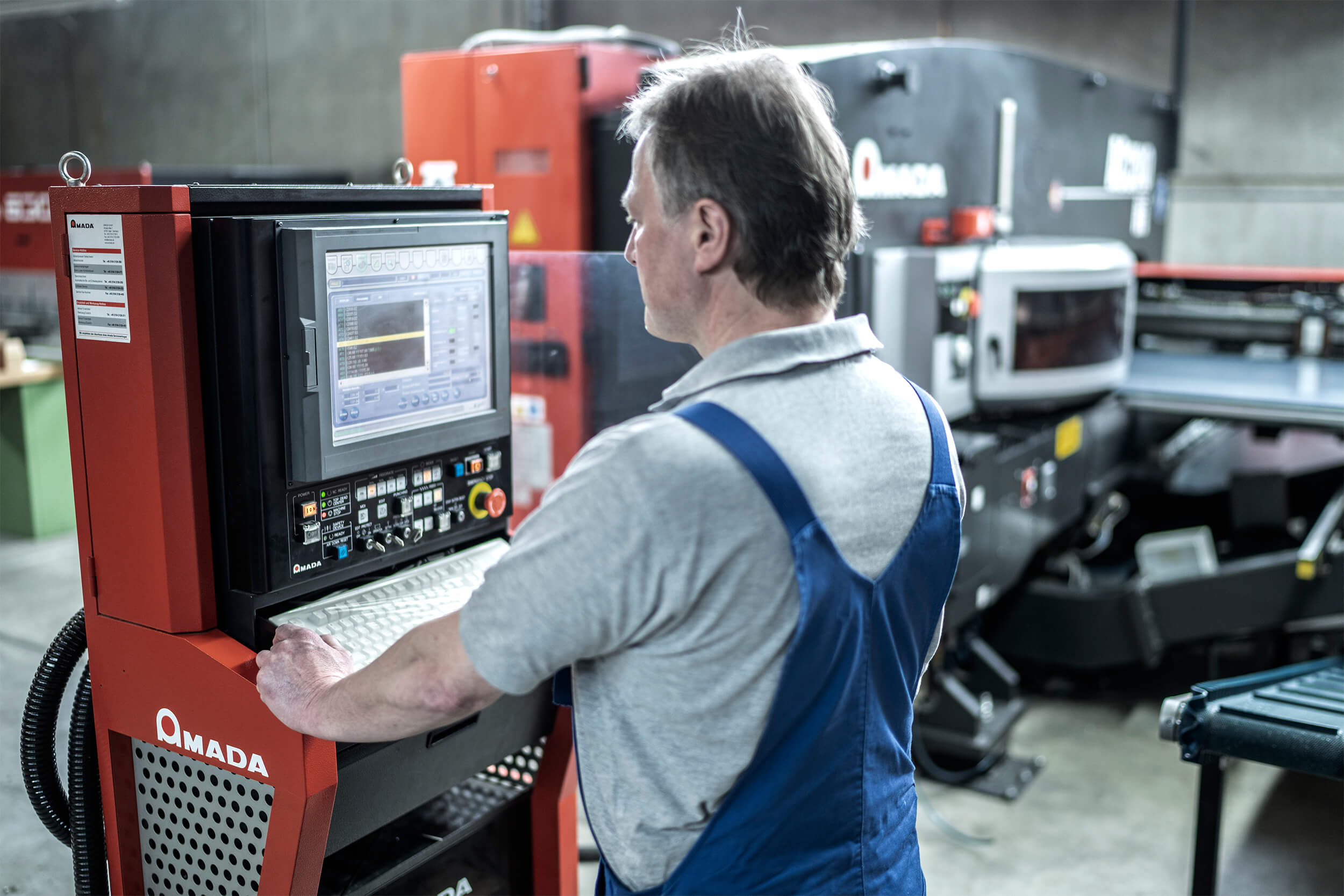
The photo shows the programming of our turret punching machine.
After the CAD configuration of the operating and display panels in the sales department, the V2A cut sizes are made in our sheet metal processing center. All punchings are made here.
The turret punching machine used at KRONENBERG has a punching force of 200KN and includes a tool turret for 51 different tool stations in total.
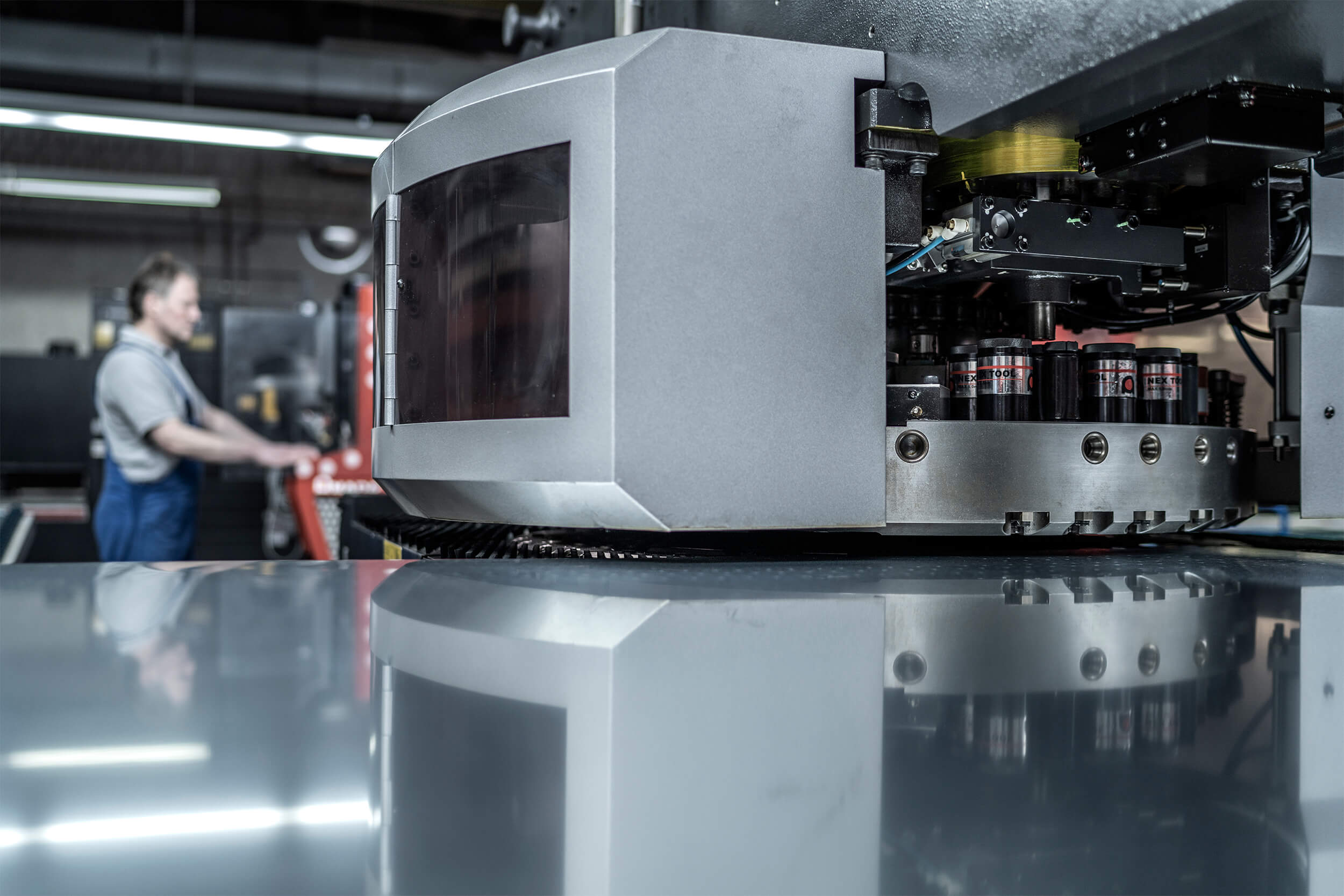
The photo shows the programming of our turret punching machine.
In the next step the pre-cut sheet metal is transported to the laser machine. The larger cut sizes for which no punching tools are available are made here, e.g. the outer contours of the panels or larger cuts for floor position displays and information fields.
The laser cutting center in use at KRONENBERG has a laser power of 2.5 KW and a traversing range of 2,520 mm (X), 1,550 mm (Y) and 300 mm in (Z).
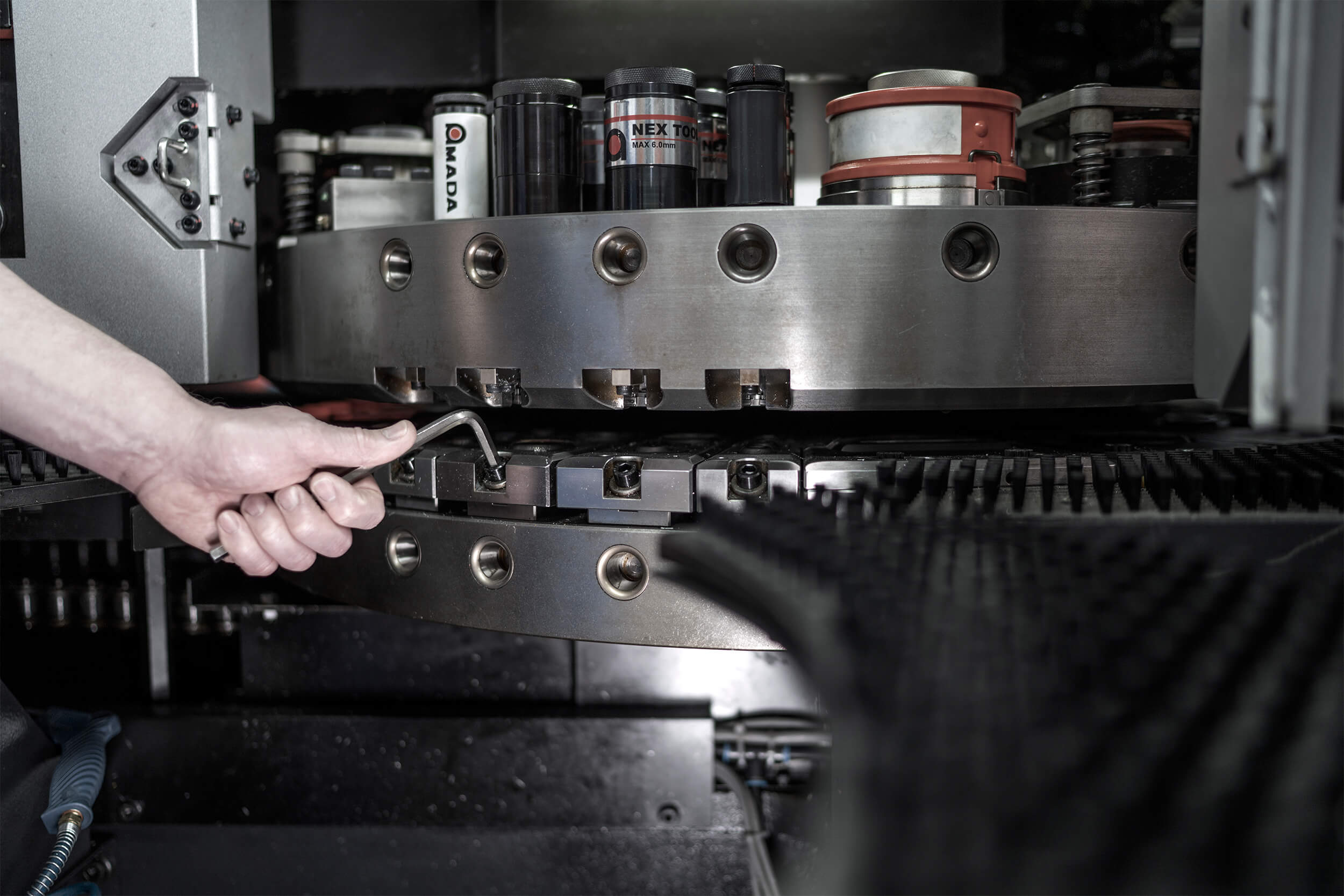
The photo shows the tool change at the turret punching machine.
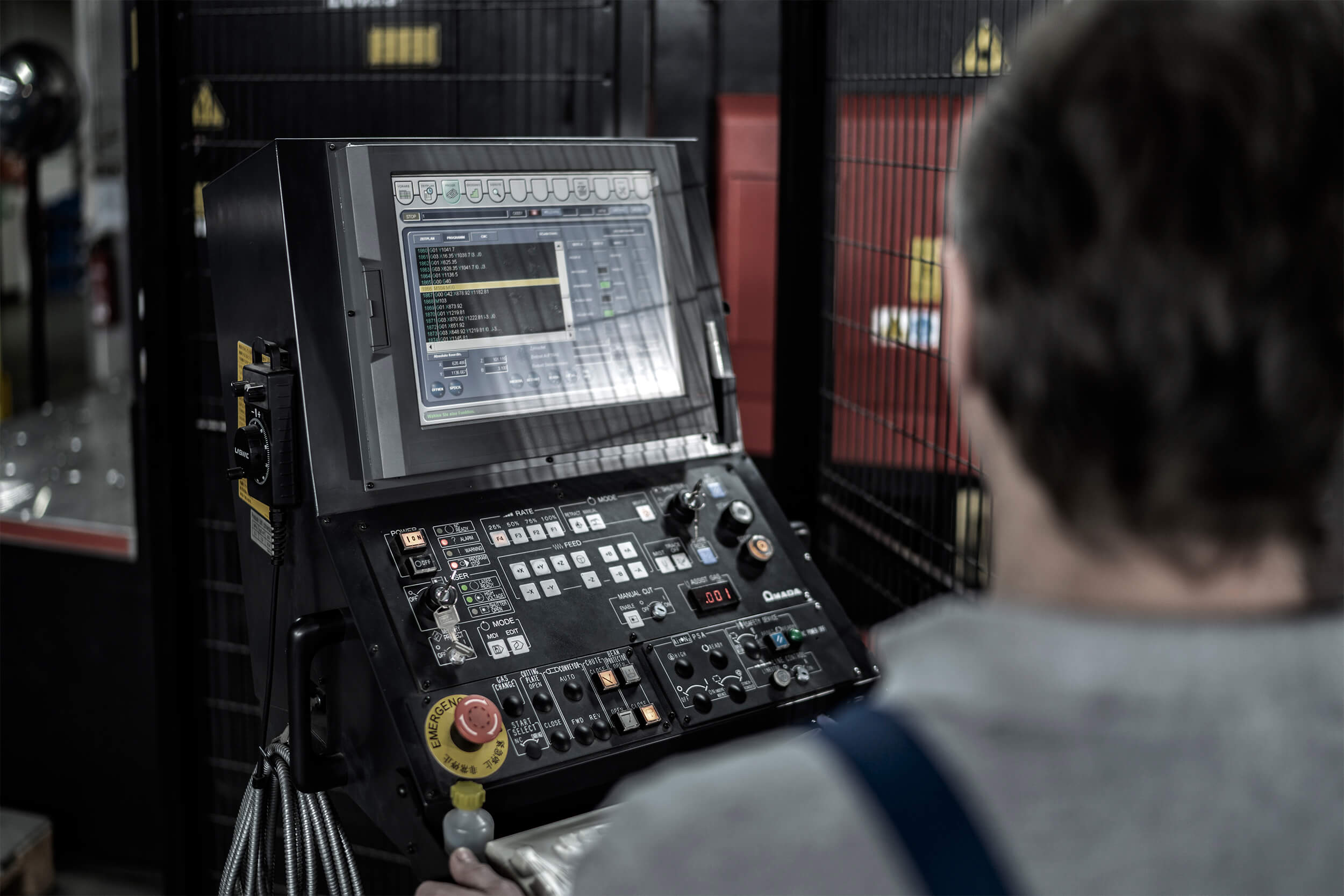
The photo shows the programming of the laser cutting center.
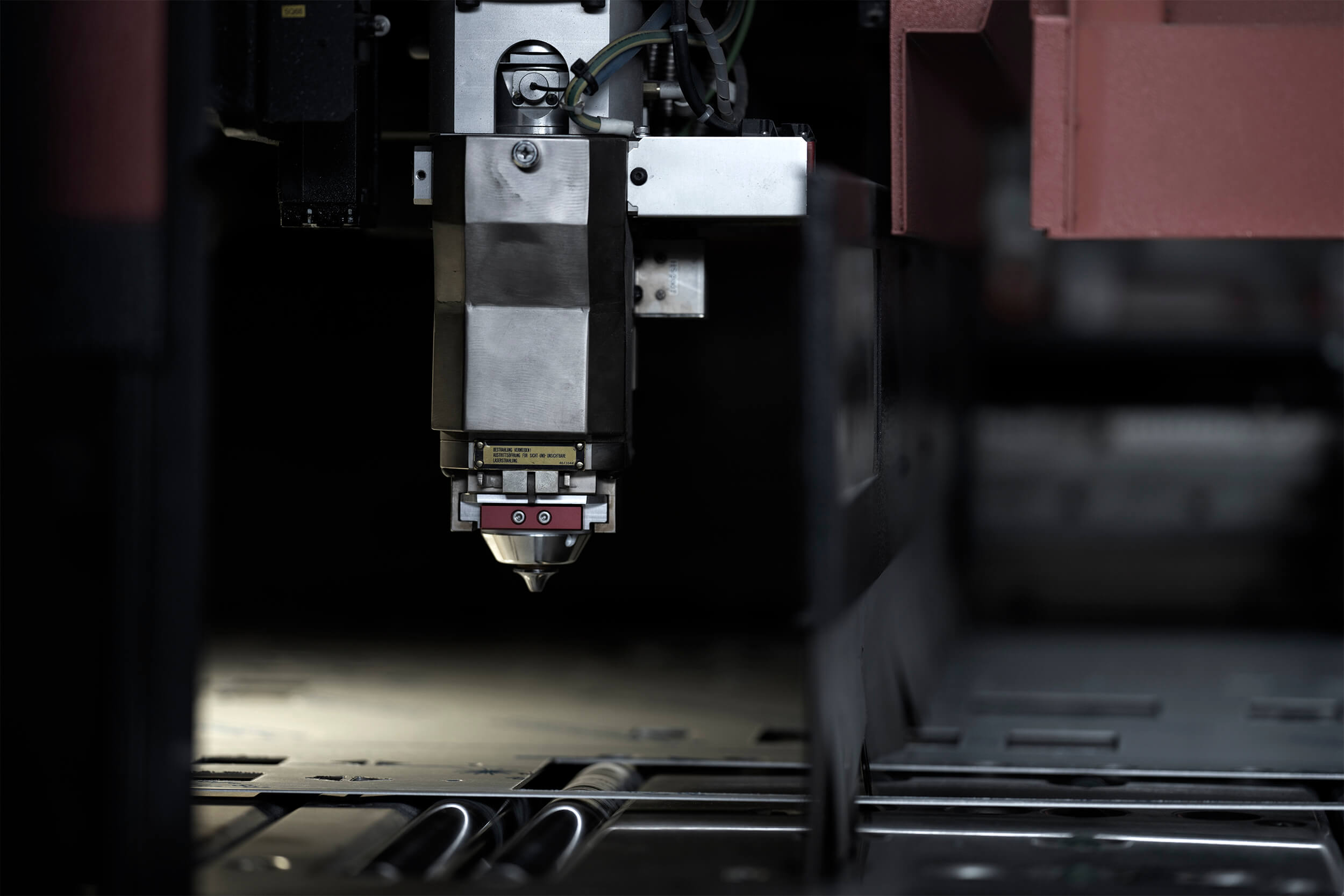
The photo shows the laser head of the laser cutting center.
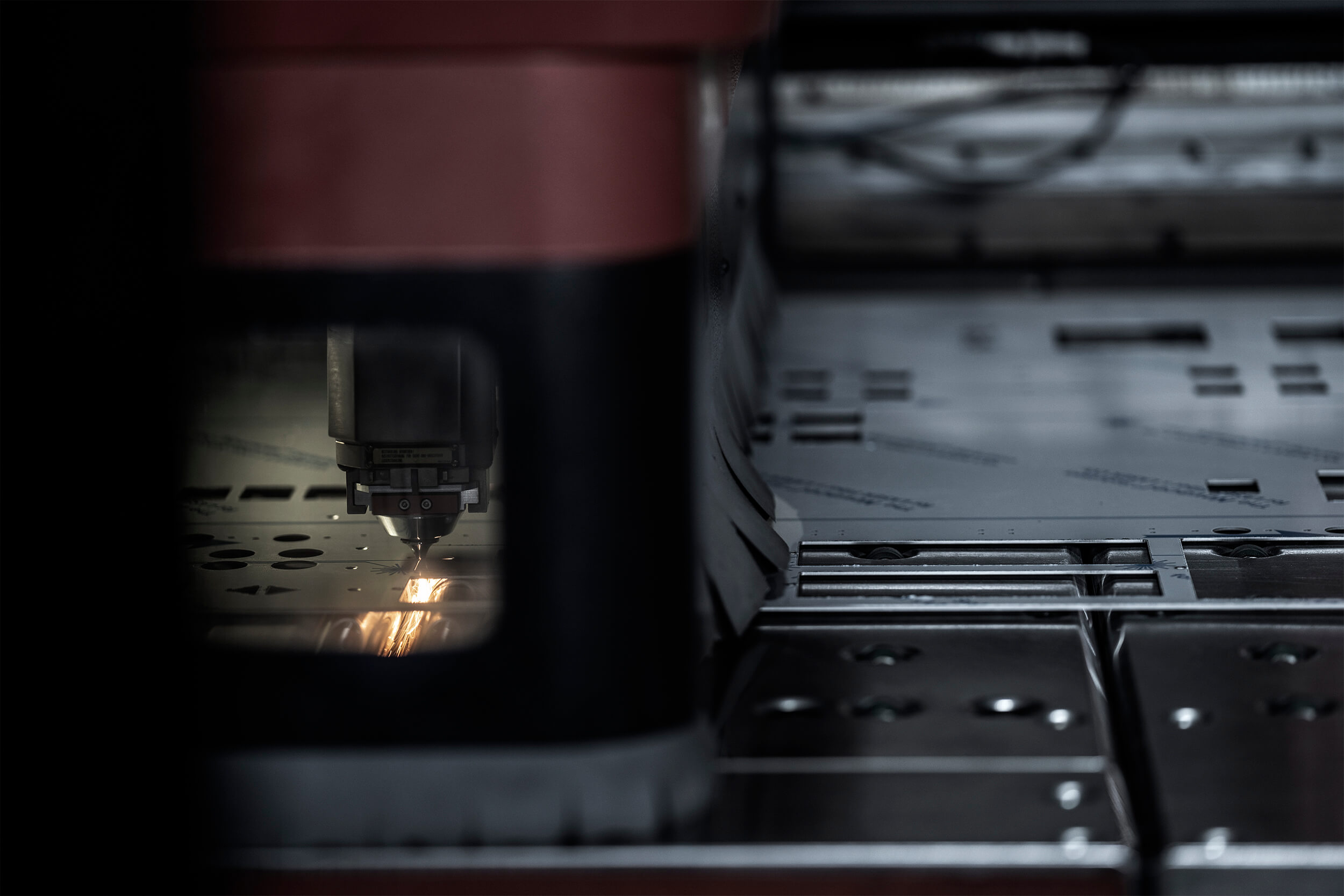
The photo shows the laser head of the laser cutting center in action.
2. Engraving room
2. Engraving room
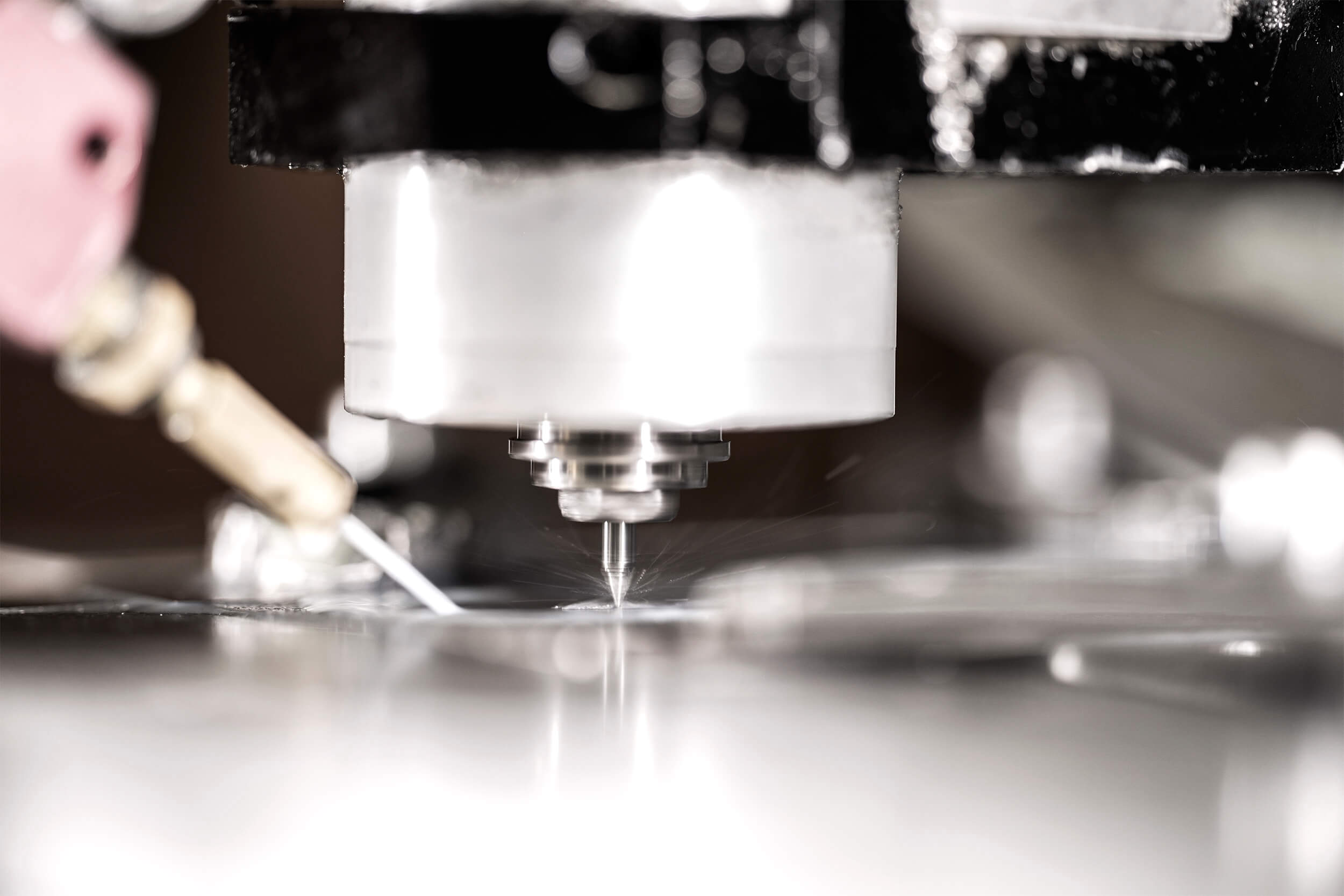
The photo shows the engraving machine during the engraving process.
In our engraving room company logos, lift symbols and common texts are milled into the already punched and cut stainless steel sheets. These letterings are then permanently filled with color.
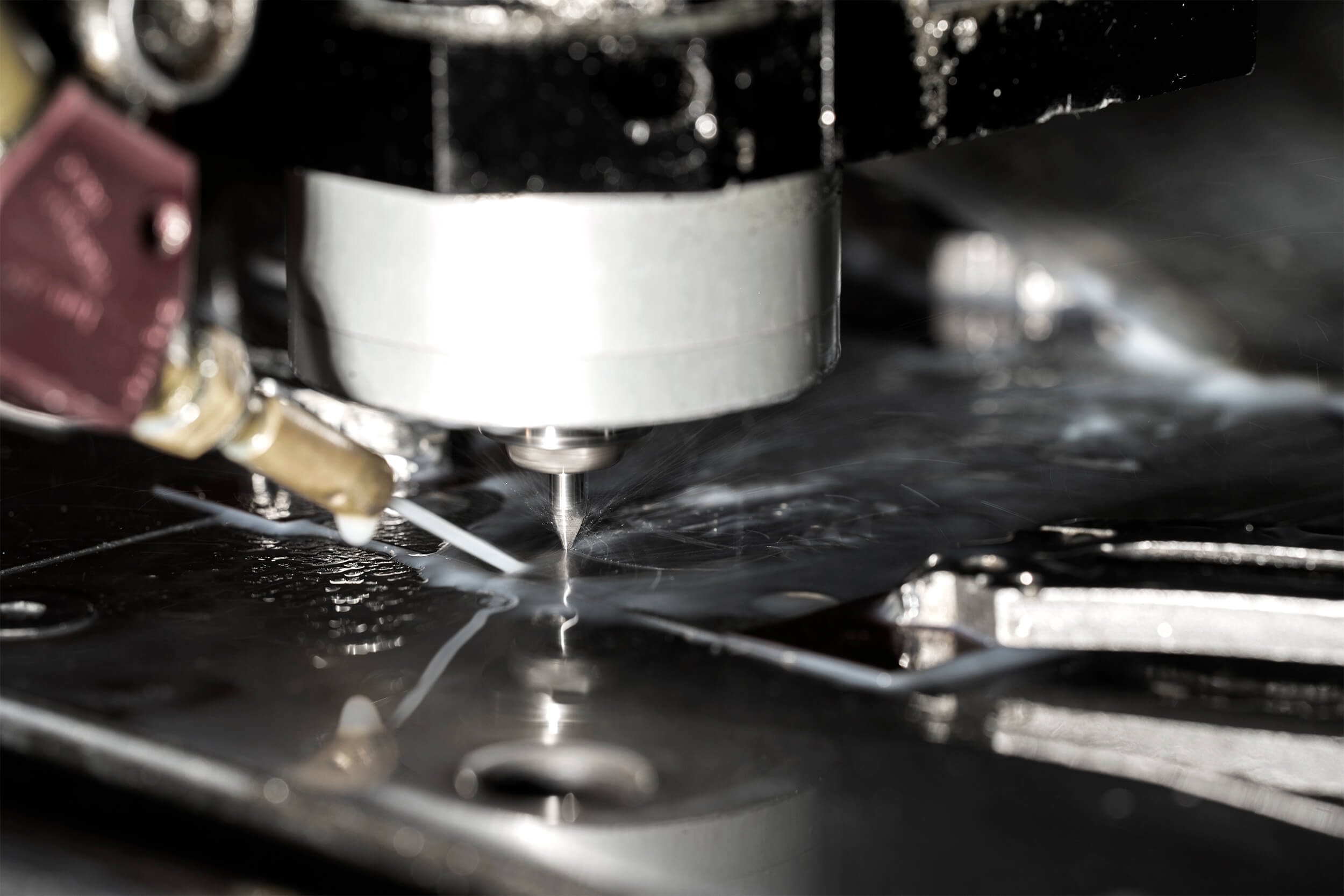
The photo shows the engraving machine during the engraving process.
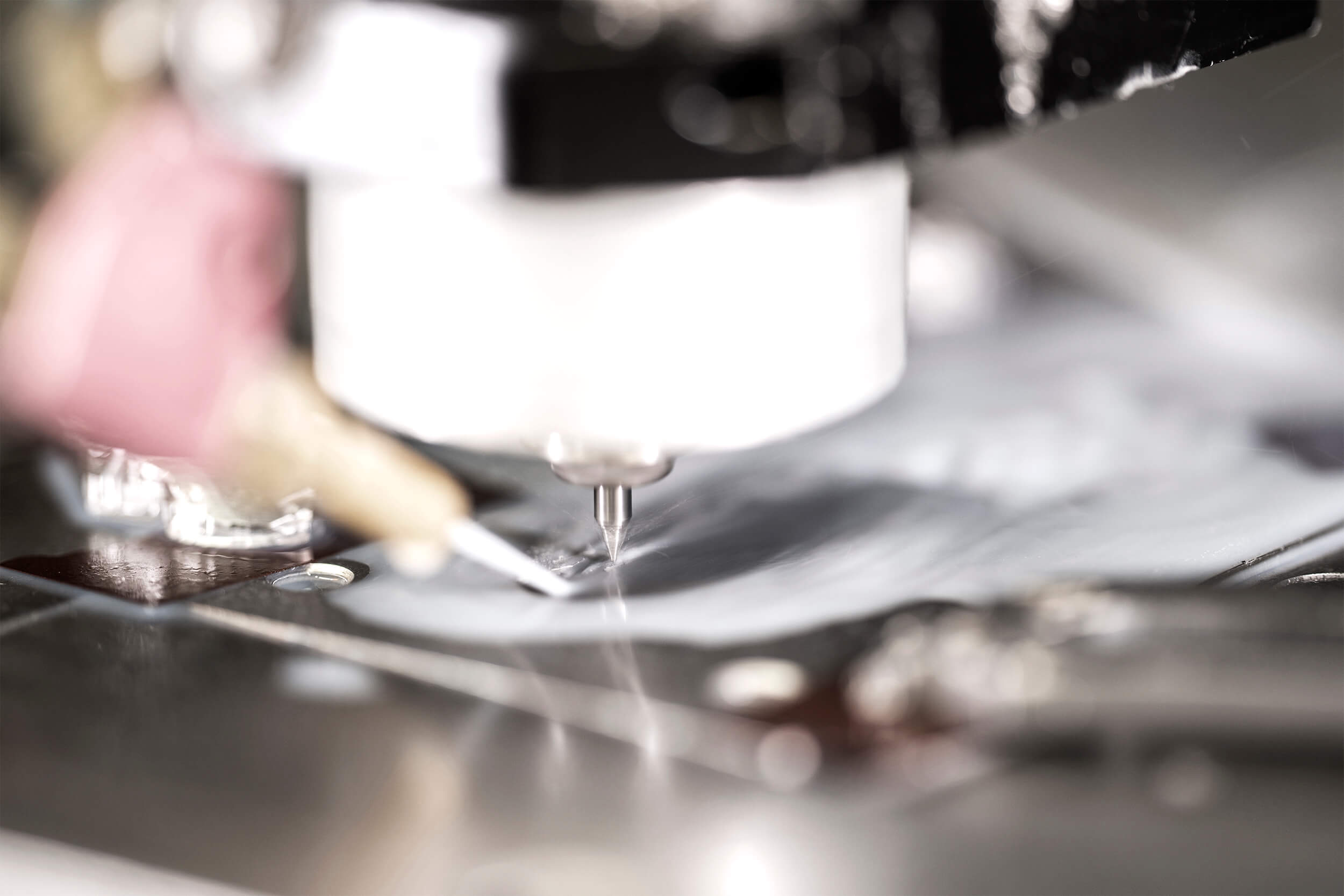
The photo shows the engraving machine during the engraving process.
3. Bending machine
3. Bending machine
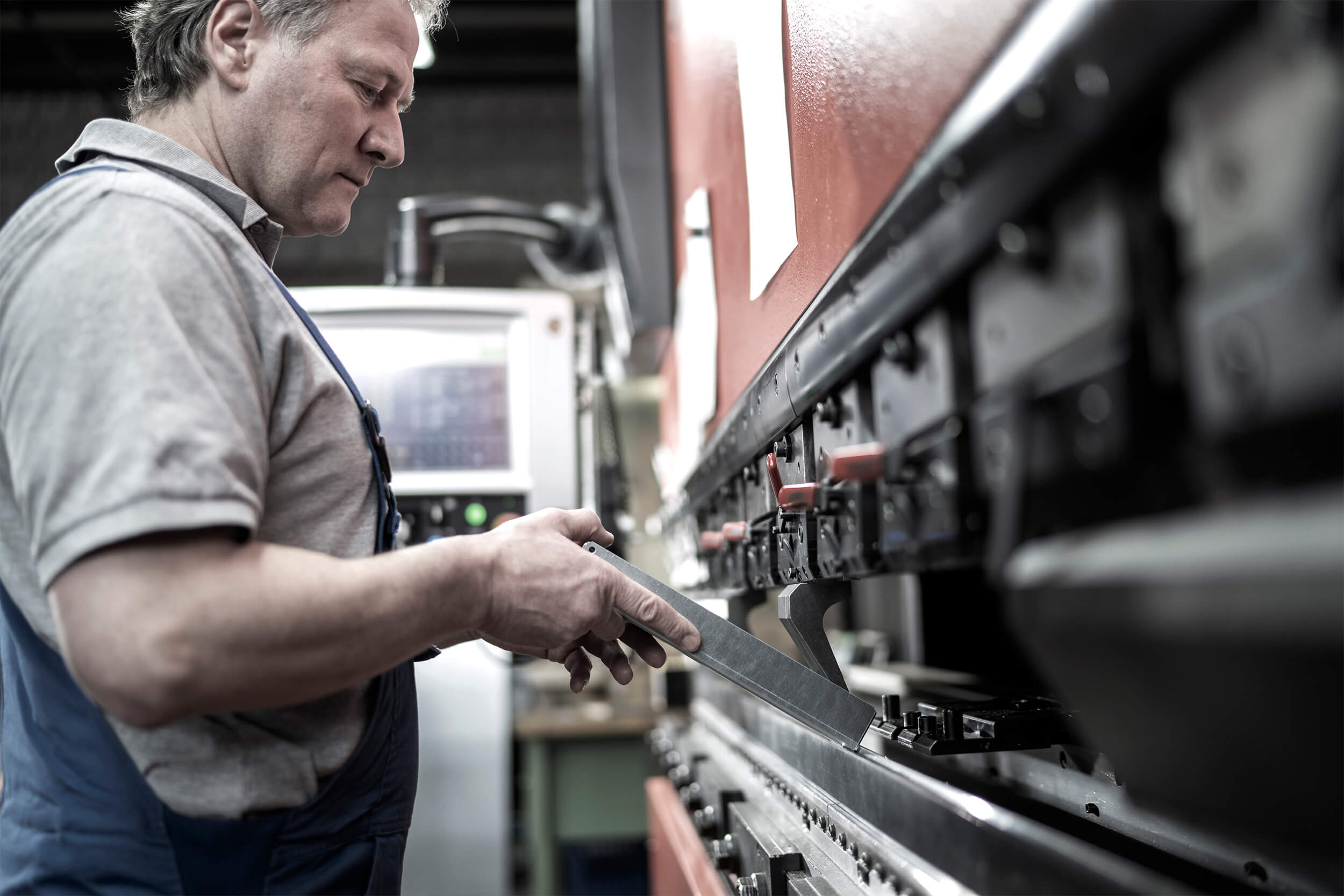
The photo shows a skilled worker at the bending machine.
In order to increase the stability of the car operating panels and panels, they are folded on the CNC-controlled bending machine.
With a pressing force of 1300 KN and a bending length of 3m, KRONENBERG can produce floor-to-ceiling panels with a sheet thickness of 3mm.
Control panels are also bent on this machine according to their processing.
DISPATCH
Versandlager
For both processes:
For both processes:
In our dispatch warehouse the final material is removed and the QR codes are scanned so that we are able to inform our customers of a delivery status just in time.
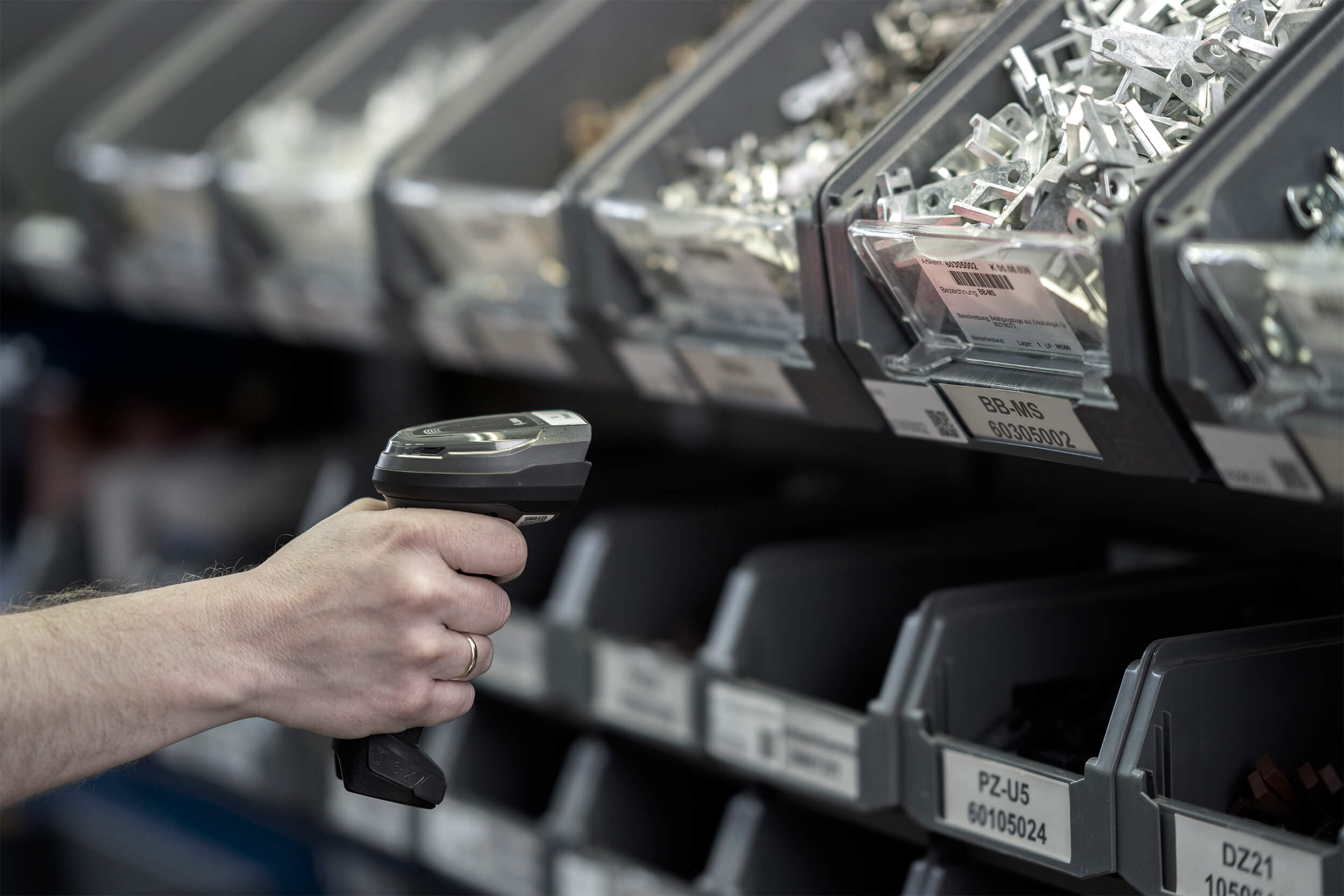
The photo shows the scanning of the goods.
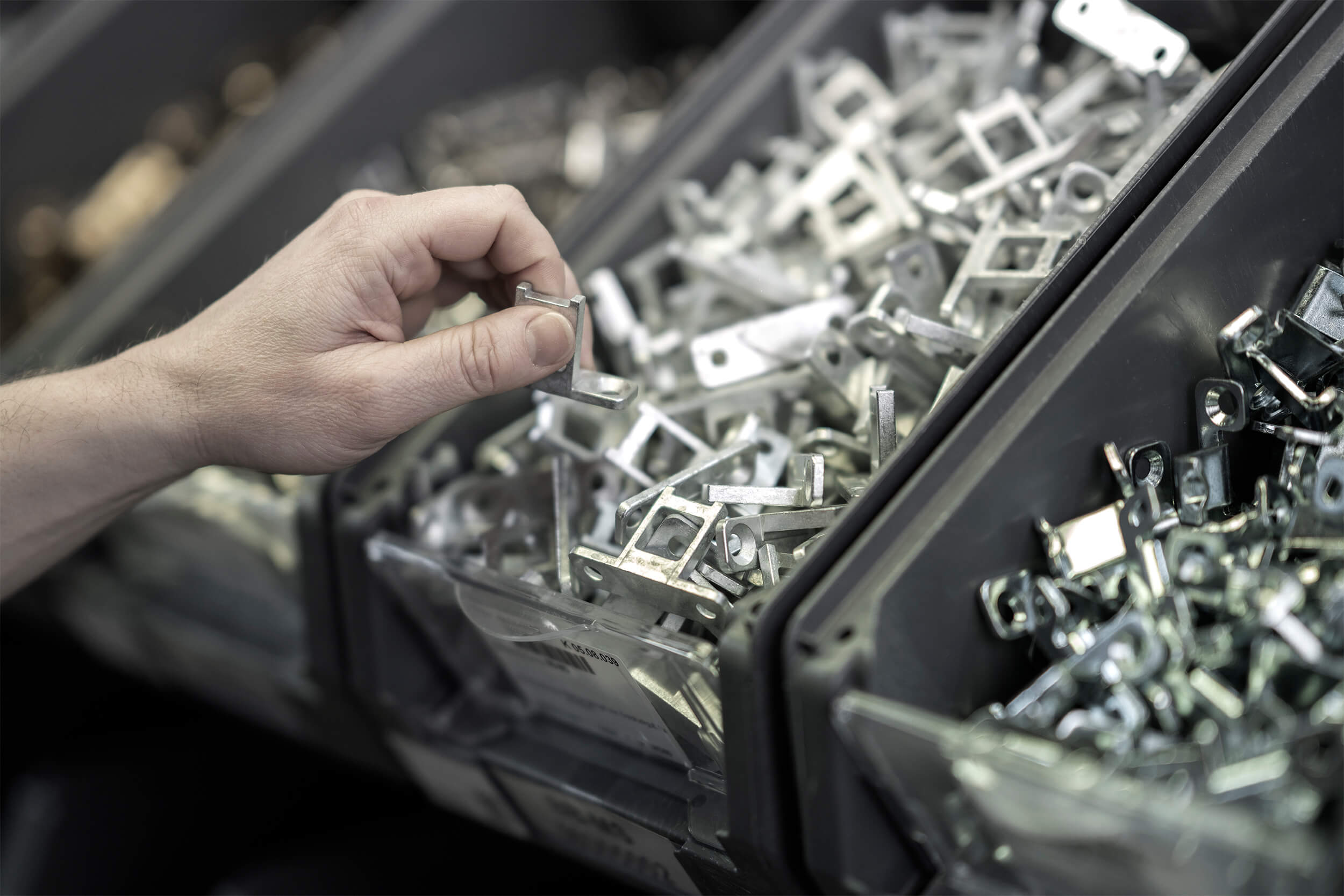
The photo shows the removal of the goods.
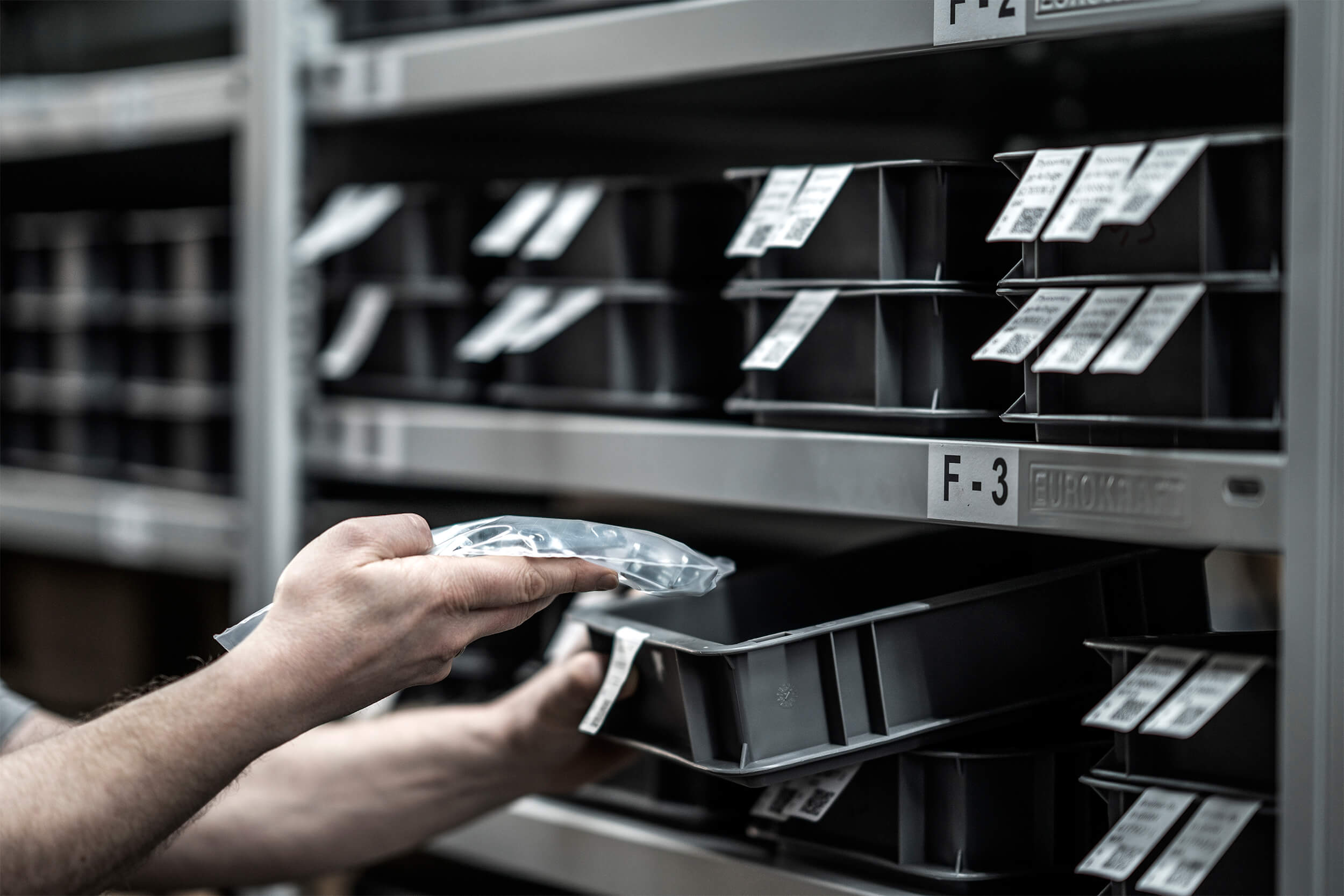
The photo shows the removal of picked goods.
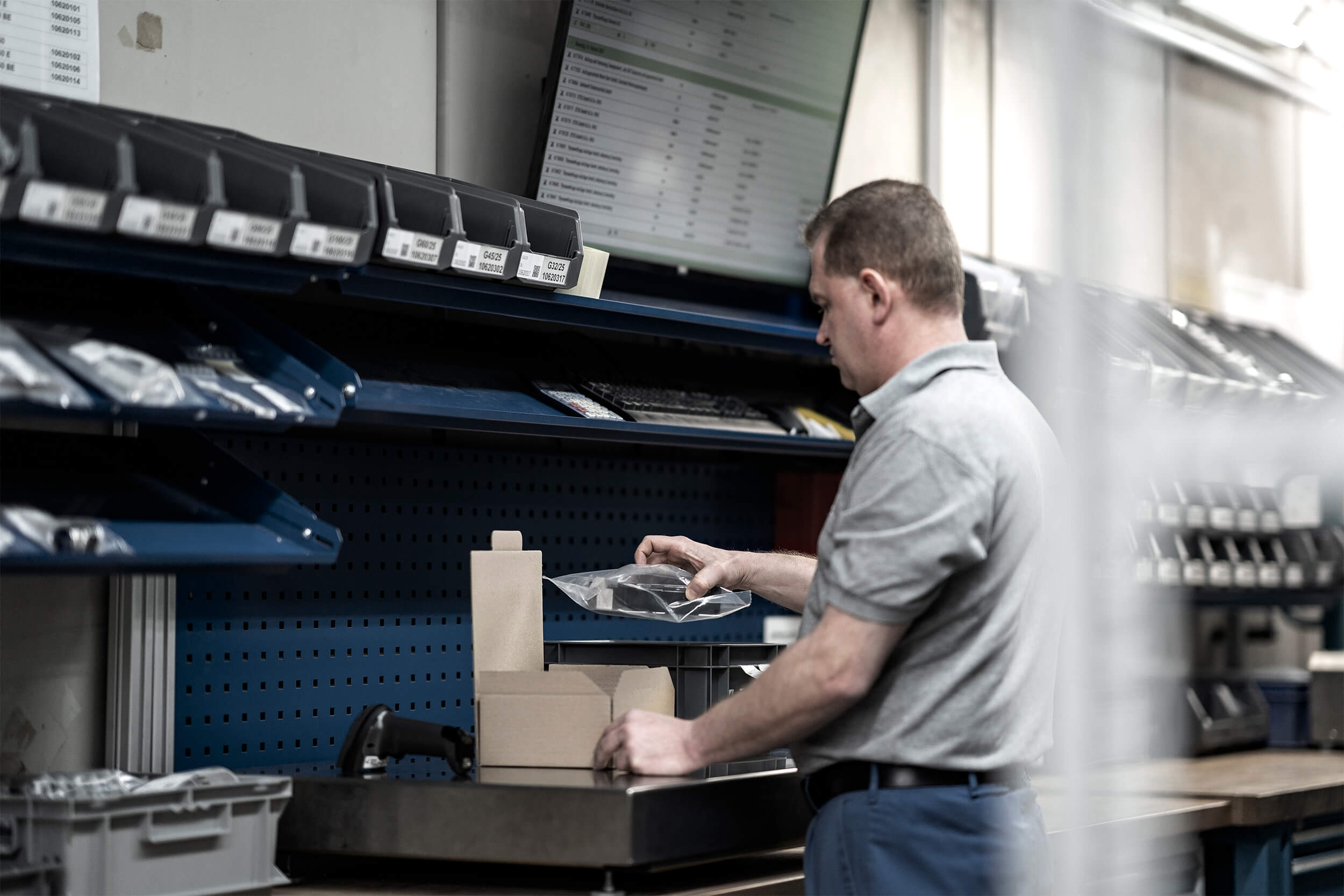
The photo shows the packing of picked goods.